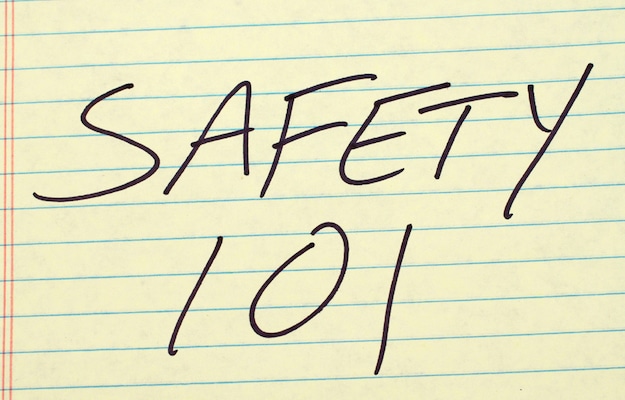
3 Safety Improvements That Will Increase OSHA Compliance | Allegiance
July 17, 2017 | Staffing Blog
OSHA employs thousands of safety inspectors who oversee over millions of work sites across the country. OSHA safety inspectors’ primary duties include accident investigations and safety consultations with companies, but they also perform surprise inspections. The last thing that any company needs are unexpected fines and safety citations.
Fall Protection
OSHA states that the lack of fall protection is the most frequently cited safety violations. Manufacturing facilities often provide adequate fall protection systems, but they may drop the ball when it comes to annual hands-on training. When an employee wearing a safety harness falls, suspension trauma may only take 10 to 15 to cause a fatality. During safety training, it’s helpful to have employees initial and date sign-in sheets for OSHA documentation. On the other hand, employees who work six feet above a surface will need adequate guardrails and personal fall protection systems.
Hazardous Communication
HAZCOM, which is the second most violated safety standard, ensures that workers are properly educated about chemicals, materials and products that they are required to use. Annual HAZCOM training will not likely be sufficient because suppliers change just like workers often cross-training in different positions. Regular communication about product updates is important. OSHA requires companies to maintain current and readily available Material Safety Data Sheet (MSDS) books for employees. This may require the support and cooperation of purchasing managers and procurement staff.
Lock-out, Tag-out
Lock-out, Tag-out (LOTO) is a must in manufacturing and production settings that use dangerous machinery and equipment. OSHA requires companies to maintain strict policies regarding maintenance safety. Authorized employees must have their own locks with their own keys. The locks must be identified by name and only supervisors have access to the key copies. Dismemberment and fatal accidents often occur when employees fail to carefully follow lock out procedures. Many safety managers and team supervisors formally discipline employees who violate LOTO policies in order to demonstrate their commitment to worker safety.
There are many OSHA rules and federal safety regulations that apply to labor-based industries. OSHA compliance can be increased through proper safety management and the support of qualified labor solutions.
Allegiance Staffing offers 25 years of experience bringing in quality employees who meet high standards. Contact us today to learn more about how our custom labor solutions can improve your bottom line. Looking for work? Join Our Talent Network Today.